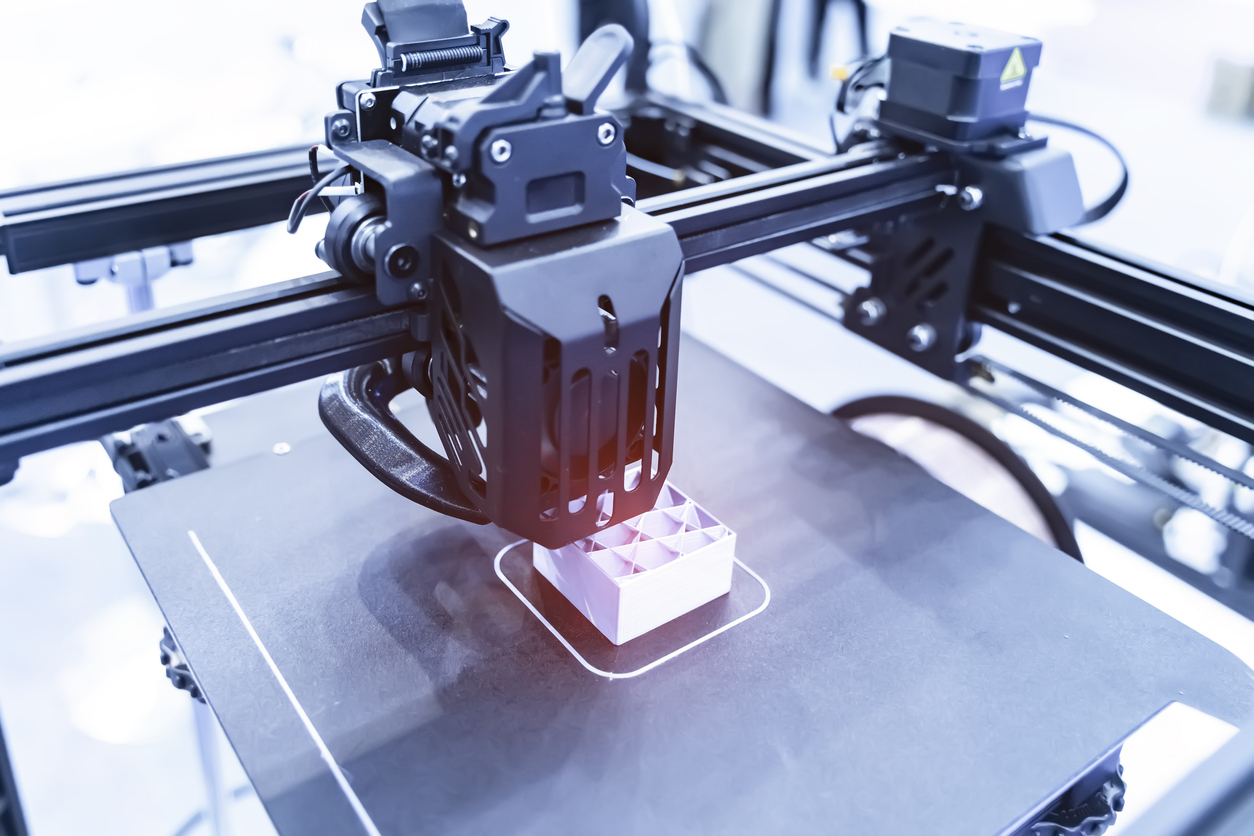
3D printing, once a niche technology used mainly for prototypes, has exploded into a transformative force across major industries. By allowing objects to be built layer by layer from digital designs, 3D printing—also called additive manufacturing—is reshaping the future of production and care. Nowhere is this revolution more visible than in manufacturing and healthcare, where customization, speed, and innovation are changing what’s possible. Here’s a deep dive into how 3D printing is impacting these critical sectors—and what the future may hold.
How 3D Printing Works (A Quick Overview)
At its core, 3D printing turns digital blueprints into physical objects by laying down material—typically plastic, metal, resin, or even biological substances—one layer at a time. Unlike traditional subtractive manufacturing (cutting or molding), 3D printing adds material only where needed, offering unprecedented precision and waste reduction.
Key benefits:
- Customization at scale
- Reduced material waste
- Rapid prototyping and production
- Lower entry costs for complex designs
Impact on Manufacturing
3D printing is transforming how products are designed, built, and distributed, impacting industries ranging from aerospace to automotive to consumer goods.
1. Rapid Prototyping and Product Development
Before:
Traditional prototyping could take weeks or months and require expensive molds and tools.
Now:
3D printing dramatically shortens design cycles by allowing companies to quickly create, test, and revise prototypes—often within a single day.
Benefits:
- Accelerates innovation
- Reduces costs associated with redesigns
- Encourages experimentation and creativity
Example:
Automakers like Ford and BMW use 3D printing to prototype parts, speeding up R&D processes and getting new models to market faster.
2. Customization and Small Batch Production
Before:
Customization was expensive and impractical for most manufacturers.
Now:
3D printing makes it feasible and cost-effective to create customized products or limited production runs without retooling entire factories.
Applications:
- Custom tools and jigs for factory floors
- Personalized consumer products like shoes, eyewear, or jewelry
- Niche market parts (e.g., vintage car replacements)
3. Supply Chain Simplification
Before:
Manufacturers relied heavily on complex global supply chains vulnerable to disruptions.
Now:
On-demand 3D printing reduces dependence on long, intricate supply lines by enabling localized production closer to end-users.
Impact:
- Reduces shipping costs and carbon footprint
- Increases resilience to global events (like pandemics or natural disasters)
- Supports faster delivery and inventory management
4. Lightweighting and Material Efficiency
Before:
Traditional methods often resulted in heavier, bulkier parts due to manufacturing limitations.
Now:
3D printing allows for innovative designs that reduce weight without compromising strength—especially important in aerospace and automotive industries.
Benefits:
- Improved fuel efficiency
- Lower transportation costs
- Enhanced product performance
Example:
Boeing uses 3D-printed titanium parts in its aircraft to reduce weight and boost fuel economy.
Impact on Healthcare
In healthcare, 3D printing isn’t just about efficiency—it’s about personalization, precision, and even saving lives.
1. Customized Prosthetics and Orthotics
Before:
Prosthetics were expensive, often uncomfortable, and time-consuming to manufacture.
Now:
3D printing allows for prosthetics that are perfectly tailored to a patient’s body at a fraction of the cost.
Benefits:
- Better comfort and fit
- Faster turnaround times
- Greater accessibility, especially in low-resource settings
Example:
Organizations like e-NABLE produce affordable 3D-printed prosthetic hands for children around the world.
2. Personalized Implants and Surgical Tools
Before:
Implants (like hip or dental replacements) were mass-produced with little customization.
Now:
Surgeons can create patient-specific implants and surgical guides that match individual anatomy perfectly.
Benefits:
- Reduced surgery times
- Better surgical outcomes
- Lower risk of implant rejection
Example:
Cranial implants, spinal cages, and even customized dental crowns are increasingly being 3D printed to fit unique patient needs.
3. Bioprinting and Tissue Engineering
Before:
Tissue engineering was experimental and heavily restricted by traditional lab techniques.
Now:
Emerging bioprinting technology enables scientists to 3D-print layers of living cells to create tissues like skin, cartilage, and even early-stage organs.
Future potential:
- Creating skin grafts for burn victims
- Printing organ patches to repair heart tissue
- Eventually printing fully functional organs for transplantation
Note:
While still in its early stages, bioprinting holds immense promise for personalized medicine.
4. Medical Training and Education
Before:
Medical training relied heavily on cadavers or generic models, which didn’t always replicate real-life patient variations.
Now:
3D-printed anatomical models allow doctors to practice surgeries or procedures on precise replicas of a patient’s anatomy.
Benefits:
- Improves training for complex or rare procedures
- Reduces medical errors
- Enhances patient-specific surgical planning
Challenges and Limitations
Despite its tremendous potential, 3D printing still faces several hurdles:
- Material Limitations: Some specialized applications require materials not yet suitable for 3D printing.
- Regulatory Hurdles: Particularly in healthcare, approval processes for 3D-printed devices can be lengthy and complicated.
- Cost for Advanced Systems: While basic 3D printers are affordable, industrial-grade and bioprinting equipment can be expensive.
- Intellectual Property Issues: Easy replication raises concerns over copyright and patent protections.
Looking Ahead: The Future of 3D Printing
The next decade will likely see:
- Increased use of sustainable, recyclable materials to make 3D printing more eco-friendly.
- Greater adoption of hybrid manufacturing (combining traditional and additive techniques).
- Advances in bioprinting that could lead to viable organs printed for transplant.
- More decentralized, on-demand production models across industries.
3D printing is no longer a futuristic concept—it’s a reality that’s reshaping manufacturing and healthcare in profound ways. By offering customization, speed, efficiency, and innovation, 3D printing empowers industries to serve people better, faster, and more affordably. As the technology advances, we’re only beginning to see how much it will revolutionize the world around us. Whether it’s a personalized prosthetic limb or a lightweight airplane part, 3D printing is proving that building the future, one layer at a time, is not just possible—it’s happening now.